What is a dosing pump?
Metering pumps are chemical pumps with low volume, which can be controlled by automatic or manual flow depending on the requirements of the work to be applied. Especially the accuracy of the pump is very high and it can pump many different chemicals such as: acid, baso, high corrosive or viscosity, etc.
Material of the metering pump
Materials exposed to liquids are PVC, PP .... teflon membrane. These materials are resistant to most chemicals. However, there are some chemicals such as acids or organic solvents, which damage elastomers and resins, such as diaphragm, valve soles or valve head. Manufacturers of plastics, elastomers and various pumping equipment provide guidance for selecting chemical pumping materials and chemical mixtures.
Principle of operation of the dosing pump
· The actuator is responsible for transmitting the rotary motion of the motor to the movement of the pump.
Pump flow can be adjusted by varying the stroke length or stroke frequency of the pump.
· Most pumps are adjusted by a screwdriver.
Hydraulic or pneumatic auxiliaries can also be used in place of screws, especially in locations where the flow rate corresponds to the control signal.
· Changing the number of pumps is also a way to increase the flow of the pump.
· Double-pump dosing pumps will increase the flow rate that can be doubled with one pump. It is even possible to install pumps with up to three or four pumps.
Quantitative pumps transport fluid through two stages, the intake and the discharge.
At the suction stage, liquid is drawn into the cavity in the chamber through the suction valve.
At the push stage, the one-way valve at the suction hose is closed, the one-way valve in the push-pull tube opens, the liquid in the pump chamber is expelled.
· Dosing pumps are usually used when one of the following conditions is used: the flow of water is too small, it is necessary to supply the liquid with the specified flow, the system is subjected to high pressure, the pump is corrosive , High temperature, high viscosity, need to adjust the flow of computer, programmers, etc.
Classification of dosing pumps
There are four types of dosing pumps depending on the different needs as follows:
1. Piston-type metering pumps
· A quantitative pump that pumps the cylinder and changes the volume of the pump chamber by the displacement of the piston inside the cylinder. The flow of the pump can be adjusted by varying the stroke length or travel frequency of the piston. The piston dosing pump is the most powerful, most stable and most powerful single dosing pump.
2. Hydraulic pump
· This is because the diaphragm is moving by transmission from a pistong that acts as a hydraulic cylinder. A new type of metering pump, the high-quality combined hydraulic pump of the two pumps, is the ability to create high pressure of the pump and the absolute tightness of the diaphragm pump. The pump chamber is separated by a flat partition (membrane pump) of rubber or plastic. The first compartment is the secondary compartment, located between the pump diaphragm and the pistong. This compartment is filled with oil. The displacement of the piston position will lead to the corresponding deformation of the diaphragm. The second compartment is the main compartment, located between the pump head and the diaphragm, which acts as the diaphragm chamber. The displacement of the pump diaphragm creates the suction or thrust of the pump fluid.
3. The pump measures the film thickness
· Many people call it "membrane pumps". Such shortcuts are wrong because most of the dosing pumps are diaphragm pumps but there are still many other diaphragm pumps other than the metering pump. The type of pump used in applications that accurately determine the amount of liquid to be supplied. Metering pumps use a diaphragm pump (usually made of rubber, but can also be made of other materials, depending on the pump material). The diaphragmatic principle is the same as that of the heart. The membrane acts as a portable heart wall. When the machine is running, the motor and the pusher will gradually push the fluid out of the membrane, creating a vacuum that pulls the liquid into the pump chamber (vacuum stroke). By the time the pump chamber is full of liquid, the pushing rod presses the membrane to pressure out the pressure. The flow direction is achieved by two one-way valves. One valve at the intake line of the pump, called the suction check valve, and the other at the discharge line of the pump, is called the discharge check valve. The film dosing pump has many advantages: it allows to adjust the flow from low to high depending on the requirements of the pump with closed structure, no liquid leakage, simple pump structure, only few moving parts. Durable operation with minimal maintenance.
4. Electronic dosing pump
Also known as Metering Pump Electromagnet. This name is because the diaphragm is moving by means of an electric magnet.
Travel apps
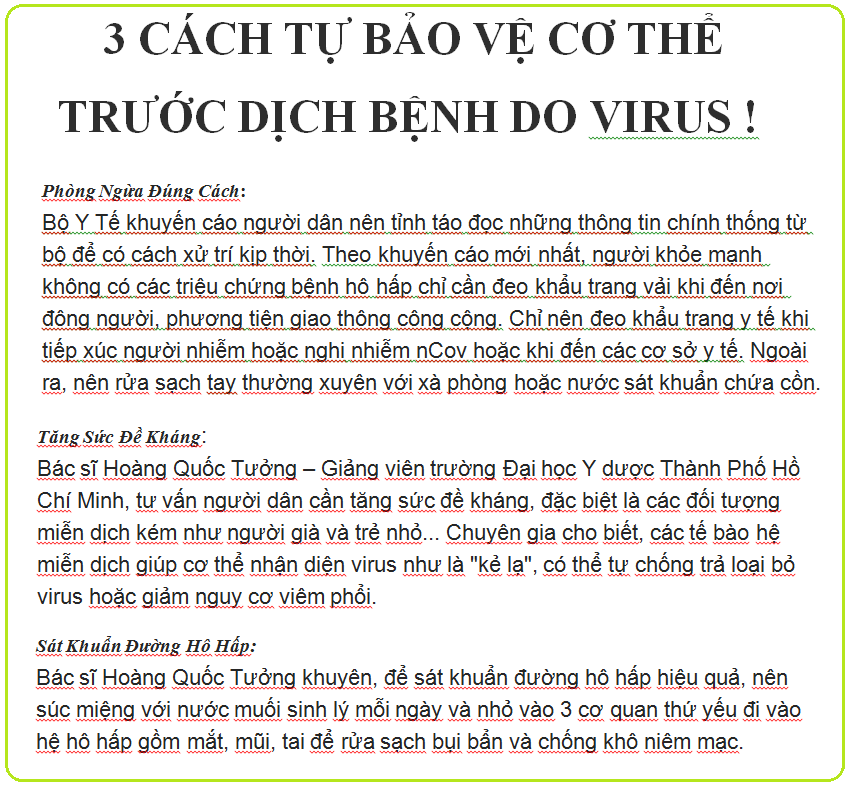
Please contact us for service
TienPhong, The supplier of Genuine Products, Professional, Reliable and Dedicated.